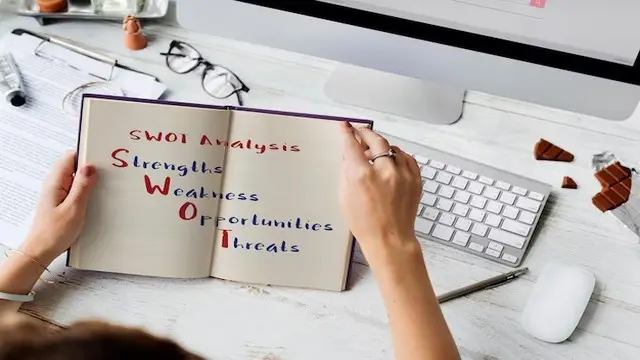
Lean Six Sigma Yellow Belt
Instant Access | CPD Group Certified | Free Digital Certificate | Free Exam | Lifetime Access
Course Line On Demand
Summary
- Reed Courses Certificate of Completion - Free
- Tutor is available to students
Add to basket or enquire
Overview
Lean Six Sigma Yellow Belt Online Training
Are you interested in enhancing your problem-solving and process improvement skills? Do you want to make a significant impact in your organization's efficiency and effectiveness? If so, the Lean Six Sigma Yellow Belt course is designed for you.
Lean Six Sigma is a proven methodology that combines the principles of Lean manufacturing and Six Sigma quality management to eliminate waste, reduce variation, and improve overall business performance. The Yellow Belt level is the entry point for individuals seeking to develop a foundational understanding of Lean Six Sigma concepts and techniques.
This comprehensive course offers a structured learning experience that covers essential topics, tools, and methodologies. It is ideal for professionals from various industries, including manufacturing, healthcare, finance, and service sectors, who are looking to enhance their problem-solving abilities and contribute to process improvement initiatives.
Throughout the course, you will embark on a journey through the various phases of the Lean Six Sigma DMAIC (Define, Measure, Analyze, Improve, Control) framework. Starting with an introduction to Lean Six Sigma, you will explore its history, evolution, and fundamental principles. You will also gain insights into the roles and responsibilities of a Yellow Belt practitioner.
The Define phase will guide you in understanding how to define the scope of improvement projects, identify customer needs, and develop project charters. In the Measure phase, you will learn to select appropriate process metrics, collect data effectively, and analyze process maps. Statistical process control (SPC) and measurement system analysis (MSA) will be introduced to ensure accurate measurement and analysis.
Moving on to the Analyze phase, you will acquire techniques for identifying root causes, analyzing data using tools such as Pareto charts and cause-and-effect diagrams, and implementing value stream mapping. The Improve phase will provide you with skills in generating improvement ideas, utilizing Lean techniques, designing experiments, and implementing mistake-proofing strategies.
In the Control phase, you will learn to implement statistical process control (SPC), monitor process performance through control charts, and develop strategies for sustaining Lean improvements. Additionally, the course includes practical case studies, exercises, and group discussions to reinforce your learning and provide real-world application opportunities.
To evaluate your understanding and prepare for the Yellow Belt certification, the course concludes with exam preparation sessions, including mock exams and practice questions. You will gain confidence in your knowledge and readiness to become a certified Lean Six Sigma Yellow Belt.
By the end of this course, you will have a strong foundation in Lean Six Sigma principles and techniques, enabling you to contribute to process improvement initiatives within your organization. You will be equipped with the skills to identify and eliminate waste, reduce variation, and enhance overall process efficiency and effectiveness.
Key Features:
- Comprehensive curriculum covering all phases of the DMAIC framework (Define, Measure, Analyze, Improve, Control).
- In-depth understanding of Lean Six Sigma principles, concepts, and methodologies.
- Exploration of the history, evolution, and benefits of Lean Six Sigma.
- Identification of customer needs and requirements through Voice of the Customer (VOC) analysis.
- Development of project charters and stakeholder analysis for effective project management.
- Selection of appropriate process metrics and data collection methods.
- Proficiency in process mapping, flowcharting, and measurement system analysis (MSA).
- Introduction to statistical process control (SPC) and data analysis techniques.
By the end of this course, you will:
- Possess a solid understanding of the Lean Six Sigma methodology and its application to process improvement.
- Be capable of developing project charters, conducting stakeholder analysis, and managing improvement projects from initiation to closure.
- Have hands-on experience through real-world case studies, practical exercises, and simulations that simulate real-life scenarios.
- Possess the ability to work collaboratively in a team setting, engaging in group discussions and problem-solving exercises.
- Be well-prepared for the Yellow Belt certification exam, with comprehensive exam preparation sessions and practice questions.
Join us in the Lean Six Sigma Yellow Belt course and unlock the potential to make a positive impact on your organization's success. Start your journey towards becoming a skilled problem solver and process improvement specialist today!
Curriculum
-
disclaimer 01:00
-
Lecture 1: Introduction to Lean Six Sigma 15:00
-
Lecture 2: Define Phase 19:00
-
Lecture 3: Measure Phase 19:00
-
Lecture 4: Analyse Phase 18:00
-
Lecture 5: Improve Phase 18:00
-
Lecture 6: Control Phase 18:00
-
Lecture 7: Case Studies and Practical Application 13:00
-
Lecture 8: Exam Preparation and Certification 14:00
-
Assessment 11:00
Course media
Description
Why you should choose Course Line
We are one of the most prestigious learning providers and are certified by UKRLP & CPD Group. We have taught over 20,000+ students!
- 5-Starrated provider
- Free course completion certificate
- No hidden fees
- Developed by an experienced Lean Six Sigma Yellow Belt
- Tutor support throughout your course
- 24/7 Student support
This Lean Six Sigma Yellow Belt course is ideal for you if you want to learn more about it. We've separated this course into multiple lectures, covering all essential elements. It will provide you with the skills and industry knowledge to boost your career in this field.
Lean Six Sigma Yellow Belt Course Syllabus
Lecture 1: Introduction to Lean Six Sigma
- Lesson 1 - Understanding Lean Six Sigma
- Lesson 2 - History and evolution of Lean Six Sigma
- Lesson 3 - Key concepts and principles
- Lesson 4 - Benefits and applications of Lean Six Sigma
- Lesson 5 - Roles and responsibilities of a Yellow Belt
Lecture 2: Define Phase
- Lesson 1 - Overview of the Define phase
- Lesson 2 - Identifying customer needs and requirements
- Lesson 3 - Voice of the customer (VOC) analysis
- Lesson 4 - Project charter development
- Lesson 5 - Stakeholder identification and analysis
Lecture 3: Measure Phase
- Lesson 1 - Overview of the Measure phase
- Lesson 2 - Selecting appropriate process metrics
- Lesson 3 - Data collection methods and techniques
- Lesson 4 - Process mapping and flowcharting
- Lesson 5 - Measurement system analysis (MSA)
- Lesson 6 - Introduction to statistical process control (SPC)
Lecture 4: Analyse Phase
- Lesson 1 - Overview of the Analyse phase
- Lesson 2 - Techniques for identifying root causes
- Lesson 3 - Data analysis tools (e.g., Pareto charts, cause-and-effect diagrams)
- Lesson 4 - Hypothesis testing and analysis
- Lesson 5 - Value stream mapping
- Lesson 6 - Lean waste identification
Lecture 5: Improve Phase
- Lesson 1 - Overview of the Improve phase
- Lesson 2 - Generating and evaluating improvement ideas
- Lesson 3 - Lean techniques for process improvement
- Lesson 4 - Design of experiments (DOE)
- Lesson 5 - Mistake proofing (poka-yoke)
- Lesson 6 - Implementation planning and risk management
Lecture 6: Control Phase
- Lesson 1 - Overview of the Control phase
- Lesson 2 - Statistical process control (SPC) implementation
- Lesson 3 - Control charts and monitoring
- Lesson 4 - Lean sustainment strategies
- Lesson 5 - Documentation and standardization
- Lesson 6 - Project closure and handover
Lecture 7: Case Studies and Practical Application
- Lesson 1 - Real-world case studies demonstrating Yellow Belt projects
- Lesson 2 - Practical exercises and simulations
- Lesson 3 - Application of Lean Six Sigma tools and techniques
- Lesson 4 - Group discussions and problem-solving exercises
Lecture 8: Exam Preparation and Certification
- Lesson 1 - Review of key concepts and principles
- Lesson 2 - Exam format and preparation strategies
- Lesson 3 - Mock exams and practice questions
- Lesson 4 - Yellow Belt certification process
Assessment Process
Upon completing the course, you will be required to undertake a multiple-choice evaluation in order to gauge your understanding of the material covered.
To successfully pass the assessment, candidates must achieve aminimum score of 60%. After completing the assessment, candidates will receive immediate feedback indicating whether they have passed or failed. This feedback will help you to understand your strengths and areas for improvement.
In the event that you do not achieve the minimum passing score, you will have the opportunity to retake the assessment without incurring any additional cost.
Certification
After successfully completing this Lean Six Sigma Yellow Belt course, you will get an instantFreedigital certificate.
Who is this course for?
The course is particularly beneficial for:
- Individuals who want to develop a foundational understanding of Lean Six Sigma principles and methodologies.
- Professionals who seek to enhance their problem-solving abilities and drive efficiency and effectiveness in their organizations.
- Managers and team leaders responsible for process improvement and quality management.
- Employees involved in operational roles and interested in gaining knowledge and skills to identify and eliminate waste.
- Project managers seeking to enhance their project management capabilities by incorporating Lean Six Sigma methodologies.
- Quality management professionals interested in expanding their knowledge of Lean Six Sigma and its application in process improvement.
- Continuous improvement specialists looking to refresh their understanding and gain a recognized Yellow Belt certification.
- Individuals aspiring to advance their careers in roles related to process improvement, quality assurance, and operational excellence.
- Professionals in industries such as manufacturing, healthcare, finance, service sectors, and any other industry where process efficiency and quality are critical.
- Anyone interested in developing practical problem-solving skills and contributing to organizational success through Lean Six Sigma principles.
Requirements
Requirements for the Lean Six Sigma Yellow Belt course are flexible, and participants with various backgrounds and experience levels can benefit from the training.
The primary prerequisites include:
Basic Understanding of Business Processes
Familiarity with Problem-Solving Concepts
Access to a computer or device with a stable internet connection
Career path
Here are some common career paths and their corresponding salary ranges:
Process Improvement Specialist/Analyst (£25,000 to £50,000 per year)
Quality Assurance Manager (£35,000 to £70,000 per year)
Operations Manager (£40,000 to £80,000 per year)
Continuous Improvement Manager (£45,000 to £90,000)
Lean Six Sigma Consultant (£50,000 to £100,000 per year)
Questions and answers
Currently there are no Q&As for this course. Be the first to ask a question.
Certificates
Reed Courses Certificate of Completion
Digital certificate - Included
Will be downloadable when all lectures have been completed.
Reviews
Currently there are no reviews for this course. Be the first to leave a review.
Legal information
This course is advertised on reed.co.uk by the Course Provider, whose terms and conditions apply. Purchases are made directly from the Course Provider, and as such, content and materials are supplied by the Course Provider directly. Reed is acting as agent and not reseller in relation to this course. Reed's only responsibility is to facilitate your payment for the course. It is your responsibility to review and agree to the Course Provider's terms and conditions and satisfy yourself as to the suitability of the course you intend to purchase. Reed will not have any responsibility for the content of the course and/or associated materials.